Introduction
The laboratory of the laboratory department is a clinical medical laboratory, which mainly tests and analyzes body fluids such as blood, saliva, and urine. There are six experimental departments and a blood bank, including clinical inspection, microbiology, biochemistry, immunity, and AIDS testing points.
The main work of the department is to provide accurate and scientific testing basis for clinical diagnosis of diseases, tracking of efficacy and estimation of prognosis from biochemistry, cytology, hematology, immunology, etc. for various diseases; from pathogens to clinical drug sensitivity tests and bacterial resistance monitoring, provide clinical recommendations for the rational use of antibiotics, etc.
Testing equipment
The testing equipment of the laboratory of the hospital laboratory department includes: biochemical analyzer, blood cell analyzer, coagulation meter, urine sediment, centrifuge, pure water machine, printer, chemiluminescence machine, plate washer, microscope, water bath, incubator, refrigerator, biological safety cabinet, computer, etc.
Main functional areas
The main functional spaces of the hospital laboratory include: specimen receiving area, emergency treatment area, body fluid collection area, instrument room, biochemical immunoassay room, AIDS screening room, drug preparation room, PCR laboratory, microbiology room, culture room, clean room, etc.
Design plan
Whether the internal space design of the hospital laboratory is reasonable will directly affect the workflow, internal communication and work efficiency. The general principle of design is to reduce unreasonable artificial obstacles as much as possible and design the laboratory environment into a beautiful, generous, safe, comfortable and efficient place.
The water supply and drainage system, power system, lighting, ventilation and heating system, and disinfection and infection control system should also be fully considered during the design. Whether the network management facilities layout of these systems is reasonable will directly affect the safety of the laboratory and even the accuracy of the test results.
1. Plane layout requirements
The laboratory is generally set up in the outpatient building and should be a separate area; the plane layout of the laboratory should be able to clearly divide the contaminated area, semi-contaminated area and clean area, and there should be physical isolation between the areas.
The contaminated area is mainly composed of testing laboratories and blood collection rooms;
The semi-contaminated area is mainly composed of auxiliary function rooms such as reagent warehouses and water preparation rooms;
The clean area is mainly composed of offices and changing rooms.
The laboratory should ensure that the flow of people and goods is separated. Personnel and items should have independent entrances and exits. In particular, pollutants should have a dedicated exit and must be sent to the designated storage point for centralized medical waste in the hospital via the hospital’s dedicated waste elevator. It is strictly forbidden to use the hospital’s passenger elevator for transportation.
(1)HIV initial screening laboratory: Divided into clean area, semi-contaminated area, and contaminated area, with an area of not less than 45 square meters.
(2)Microbiology laboratory: Divided into preparation room, buffer room and work area, with an area of not less than 35 square meters.
(3)PCR laboratory: Divided into reagent preparation room, sample preparation room, and amplification analysis room. A buffer room should be set up at the front of each laboratory, with a total area of not less than 60 square meters.
(4)Biochemical area: When designing, the biochemical machine should be the focus. The biochemical machine is updated very quickly. Before designing, the equipment manufacturer should be contacted to determine the equipment placement, weight, specifications, water consumption, power and other parameters.
(5)Blood collection area: It is recommended to design a separate area. The length of the blood collection window should not be less than 1.2m and the width should be 45-60cm. The number of blood collection windows should be determined based on the average daily outpatient number and the needs of future business development should be appropriately considered.
(6)Instrument room: The pretreatment room and instrument analysis room are separated; different types of sample processing rooms are separated; different types of instrument rooms that may interfere with each other are separated.
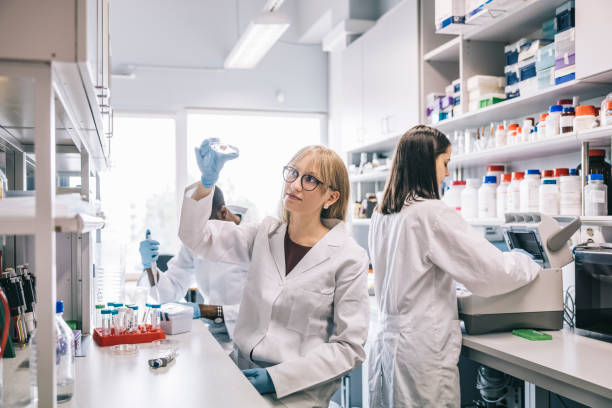
2. Indoor decoration and cleanliness requirements
(1)Floor material: It is required to use seamless anti-slip and corrosion-resistant floors. Commonly used decorative materials are rubber or PVC floors. The joints of the paving should be welded with the same color solder and planed and polished.
(2)Ceiling and wall panel materials: Easy to clean, disinfect, dust-free, crack-free, smooth, waterproof, and scrub-resistant. Commonly used materials are double-sided sandwich color steel plates with a fire protection level not lower than flame-retardant B1.
(3)Laboratory door requirements: Should be able to close automatically, an observation window should be installed on the door, with a door lock and door closer, and a working status indicator light can be installed on the door head to indicate whether someone is working in the laboratory.
(4)Laboratory window requirements: Openable external windows should not be installed on the wall, but closed observation windows can be installed.
(5)Joints between laboratory walls: The joints between the wall and the ground, and the joints between the wall and the ceiling should be rounded, and the joints of the color steel plates should be treated with sealant to ensure the airtightness of the laboratory.
(6)Laboratory ceiling height requirements: The ceiling height should be 2.6m, and inspection holes should not be opened in the main laboratory ceiling.
3.Requirements for ventilation and air conditioning engineering
(1)Purification laboratories should avoid the situation where multiple laboratories share one air conditioning unit. Independent air conditioning units can effectively avoid cross contamination and save operating costs.
(2)The design parameters of laboratory air conditioning should refer to the requirements of the “Technical Specifications for Biosafety Laboratory Buildings”. The heat and humidity loads of equipment such as biosafety cabinets, centrifuges, and incubators should also be considered during the design.
(3)The air purification system should be equipped with three-level air filtration: coarse/medium/high efficiency. The coarse filter should be located at the fresh air inlet, the medium filter should be located in the positive pressure section of the air conditioning unit, and the high efficiency filter should be located at the air supply end of the system.
(4)The height of the fresh air inlet should not be less than 2.5m from the ground. The fresh air inlet should have anti-rodent and anti-rain measures, and a filter that is easy to remove and clean should be installed.
(5)The laboratory’s exhaust fan should be designed to be interlocked with the supply fan. The exhaust fan should be turned on before the supply fan and turned off after the supply fan. The indoor exhaust duct and the exhaust duct of equipment such as the biosafety cabinet should be set separately.
(6)The layout of indoor air supply and exhaust vents should minimize the space where indoor air flow stagnates. The air supply and exhaust in the clean room should adopt the method of upper air supply and lower exhaust.
(7)The pressure difference between each area of the laboratory should be no less than 5Pa to ensure that the air flow flows from the clean area to the contaminated area to avoid backflow pollution. It is recommended to set up a pressure differential gauge in a place where it is easy to observe.
(8)Wood materials should not be used for air conditioning units and filters. Corrosion-resistant and non-absorbent materials should be used. The air leakage rate of air conditioning units should be less than 2%.
(9)Air conditioning mainly adopts fan coil plus fresh air system. The centralized cold and heat source of the hospital is used in winter and summer. If the hospital has no cold and heat source in spring and autumn, it can provide cold and heat source with its own air-cooled modular unit.
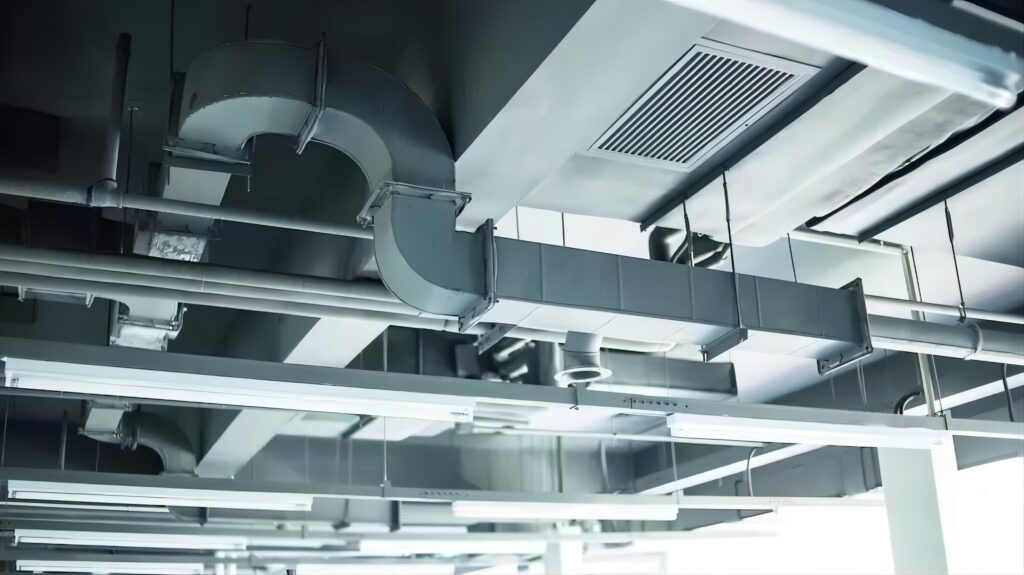
4. Electrical engineering requirements
The biosafety laboratory should ensure the reliability of electricity use. The load should not be lower than level 2. An uninterruptible power supply should be installed to ensure that the main equipment has a reserve power supply of no less than 30 minutes after the mains power is cut off. A sufficient number of fixed power sockets should be set up in the biosafety laboratory. Important equipment should be powered by a separate circuit and a leakage protection device should be installed.
Lighting system
(1)Laboratory illumination ≥300 lx Buffer room illumination ≥200 lx Office area illumination ≥200 lx.
(2)The laboratory should be equipped with ultraviolet sterilization lamps. One ultraviolet lamp (30W) can be equipped for every 10-15㎡.
(3)The number and location of evacuation indicator lights, emergency lights, and exit indicator lights should be set in accordance with relevant fire protection regulations.
Power distribution system
(1)When designing the electrical system, a sufficient number of sockets should be set up, and the power consumption of the main equipment in the laboratory should be understood in advance. A dedicated distribution box should be set up in the biosafety laboratory.
(2)Before designing an uninterruptible power supply, the laboratory manager should be communicated with to determine the equipment that needs to be powered by the uninterruptible power supply and the shortest power supply time. The location where the uninterruptible power supply is placed should have good ventilation conditions.
New weak current system
(1)Telephone network terminals: A sufficient number of telephone network terminals should be set up in the laboratory to meet the requirements of laboratory information management.
(2)Access control system: It can restrict the entry of unauthorized personnel and ensure the safety of the laboratory.
(3)Monitoring system: It can monitor the entry and exit of laboratory personnel, daily work conditions, video teaching, etc.
(4)Call system: An emergency call extension should be set up in the laboratory, and the call host should be set up in the duty room.
5. Requirements for water supply and drainage system
(1)Pure water system: The main equipment that uses pure water in the laboratory is the biochemical analyzer. Before designing the laboratory pure water system, the laboratory manager should communicate with the laboratory manager about the water use points and water consumption of each water point.
(2)Water supply system: A hand washing device should be installed in the biosafety laboratory, and it should be installed near the exit of the laboratory. A non-manual switch should be used for the water supply of the hand washing device. Indoor water supply pipes should be made of stainless steel pipes, copper pipes or non-toxic plastic pipes, etc., and the pipes should be reliably connected.
(3)Drainage system: Floor drains should not be installed in clean laboratories. Laboratory drainage should be separated from living area drainage, and laboratory drainage should be ensured to enter the hospital sewage treatment station.
6. Requirements for laboratory furniture
(1)Laboratory furniture can be divided into three categories according to the materials used: all-steel furniture, all-wood furniture, and steel-wood furniture. All-steel furniture is beautiful in appearance but relatively expensive. All-wood furniture is rarely used due to its drawbacks in load-bearing and waterproofing. Steel-wood furniture is relatively moderate. When designing, appropriate furniture should be selected in combination with the hospital’s cost budget.
(2)The main materials of laboratory countertops are epoxy resin board, solid physical and chemical board, and Trespa board. Since there are not many high-temperature equipment used in the laboratory of the laboratory, solid physical and chemical board countertops and Trespa board countertops are generally recommended.
(3)Before making the laboratory table, the style and length/width should be determined based on the actual situation on site and work needs. Insufficient furniture will affect the work, and too much furniture will take up too much work space.
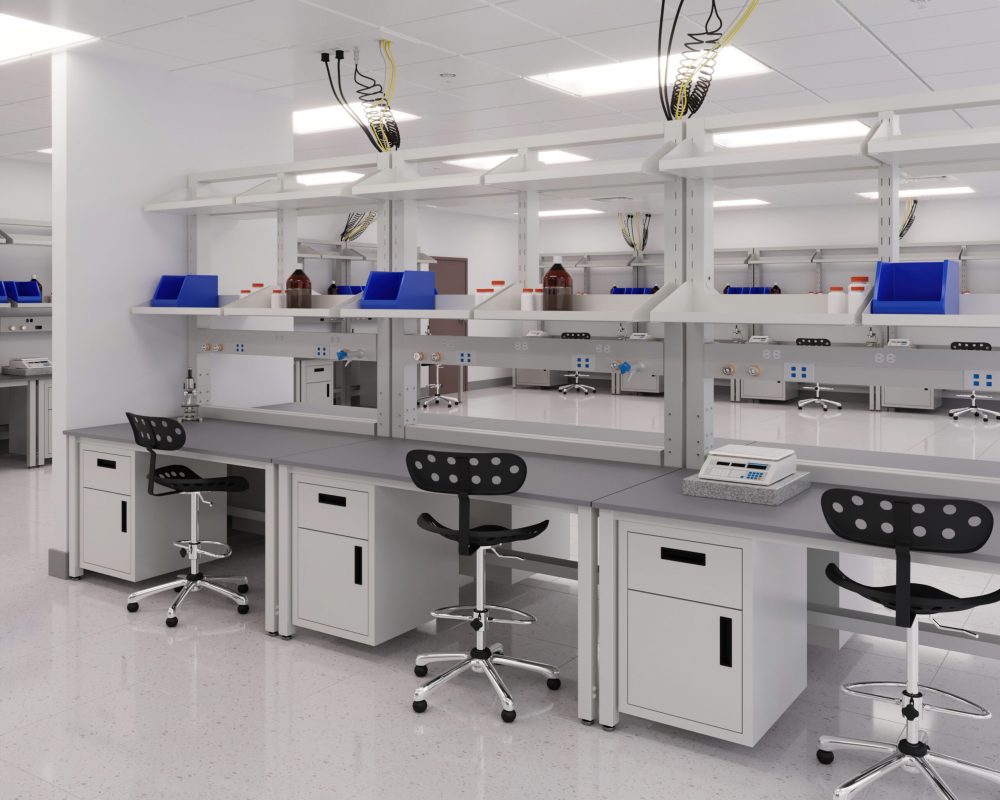
Conclusion
The laboratory is a bridge between clinical medicine and basic medicine. It is a clinical diagnosis department in the hospital that receives blood, body fluid and other samples from patients, conducts tests and analyses, and issues test reports to clinical physicians. A scientifically designed laboratory can provide a safe and efficient working environment for test personnel.
Why Choose Us?

CNMEDITECH is dedicated to the long-term research of the medical equipment market. Our mission is “People oriented and win-win strategy,Matching the real needs of the region with a focus on human health,To be the world’s first-class medical field solution expert”.We have been manufacturing high-quality medical device products for more than ten years.
We have built our reputation on delivering quality healthcare solutions on time and on budget.All our products comply with international health and safety regulations and all products come with a warranty.
Are you still worrying about your customer’s product needs?Are you still angry that the product is expensive? We have various medical equipment and support personalized product customization.
Our company has many styles to choose from.In addition, we have high-quality pre-sales consulting guidance and professional after-sales service, all to meet your needs.
Whether it is a cost-effective or high-end product, there will always be something suitable for you.If you have any needs for products, you can ask us, our factory will meet your needs as soon as possible, and we will make every effort to provide you with solutions.Feel free to send us your inquiries.